Mejora de la Productividad en el Área de Almacén mediante Gestión de Inventarios en una Empresa Agroindustrial en Motupe, Perú
Improving Productivity in the Warehouse Area through Inventory Management in an Agroindustrial Company in Motupe, Peru
Resumen
El objetivo de esta investigación fue implementar una gestión de inventarios para mejorar la productividad en el área de almacén de una empresa agroindustrial Motupe, 2024. La investigación es de tipo aplicada con alcance descriptivo de diseño cuasiexperimental, utilizando instrumentos para la recolección de datos como entrevistas con el jefe y los colaboradores del almacén, también análisis documentarios para la recolección de ambas variables. Se aplicaron herramientas de diagnóstico como los diagramas de Ishikawa y Pareto para identificar problemas como desorden y poca limpieza, ausencia de señalización, ausencia de indicadores de productividad, deficiente control de materiales, falta de capacitación, procesos no estandarizados. Se propuso implementar la técnica de las 5s, la clasificación ABC, determinar indicadores de productividad, crear formatos de control de salida de materiales, crear un plan de capacitaciones y un diseño de proceso de despacho. En los últimos tres meses la eficiencia fue de 94%, la eficacia de 91%, dando una productividad del 85% en el área de almacén. Se concluye que con la implementación de la gestión de inventarios la eficiencia mejoro en un 17%, la eficacia en 20% y la productividad en 31%.
Palabras clave: gestión de inventario; productividad; almacén; eficiencia; eficacia
Abstract
The objective of this research was to implement inventory management to improve productivity in the warehouse area of an agro-industrial company Motupe, 2024. The research is of an applied type with a descriptive scope of quasi-experimental design, using instruments for data collection such as interviews with the warehouse manager and collaborators, as well as documentary analysis for the collection of both variables. Diagnostic tools such as Ishikawa and Pareto diagrams were applied to identify problems such as disorder and lack of cleanliness, absence of signage, absence of productivity indicators, poor material control, lack of training, and non-standardized processes. It was proposed to implement the 5S technique, ABC classification, determine productivity indicators, create material output control forms, create a training plan, and design a dispatch process. In the last three months, efficiency was 94%, effectiveness was 91%, resulting in 85% productivity in the warehouse area. It is concluded that with the implementation of inventory management, efficiency improved by 17%, effectiveness by 20%, and productivity by 31%.
Keywords: inventory management; Productivity; warehouse; efficiency, effectiveness
1. Introducción
En el ámbito internacional se ha señalado que la teoría tradicional de inventario-producción resulta insuficiente, ya que no considera factores clave como la capacidad de transporte y la fiabilidad de los proveedores. La optimización de inventarios es clave para mejorar la competitividad en el mercado, pues permite evaluar pérdidas y reducir costos de almacenamiento con ciclos de pedidos más cortos y una mayor rotación de inventarios (Stopková et al., 2019). Sin embargo, aún no se tiene un conocimiento completo de cómo la rotación de inventarios representa un indicador clave de eficiencia, reflejando la rapidez de venta de los productos. Además, los inventarios representan uno de los mayores costos de producción para los productores (Alnaim & Kouaib, 2023).
En el caso de las empresas madereras, la administración de inventarios es ineficiente debido a la falta de integración en la cadena de suministro, ya que el 93% de estas empresas aún gestionan inventarios de forma manual, lo que impide un aprovisionamiento preciso (Salas-Navarro et al., 2017). Además, muchas empresas carecen de conocimiento sobre estrategias eficientes de gestión de inventarios; la mayoría de los procesos y registros contables se realizan manualmente, lo que dificulta la verificación de información, incrementa el riesgo de fraudes y pérdidas de productos debido a un control de ventas no optimizado (Cardoso et al., 2023).
El manejo inadecuado de existencias en almacén también está relacionado con la falta de conocimiento de la demanda, lo que provoca almacenamiento excesivo y un flujo lento de productos. La falta de control en el orden de salida de artículos aumenta el riesgo de pérdidas y disminución de calidad de los productos (Pérez-Mata & Romero-Dessens, 2022). En el ámbito nacional, se enfrentan problemas de inventarios por no usar el modelo ABC ni planificar sus procesos, y la falta de integración entre compras y abastecimiento dificulta la planificación de la demanda (Peña-Asenjo et al., 2023).
Las PYMES se encuentran en una situación crítica, sufriendo por la falta de planificación, baja productividad, retrasos, pérdidas y cuellos de botella en la producción (Bandopadhyay & Khan, 2020). De igual manera, las tiendas de muebles experimentan problemas de baja productividad debido a actividades no productivas, desorden, retrasos, distribución ineficiente y escasez de materiales (Baca et al., 2021). A pesar del crecimiento del país, la productividad del almacén es ineficiente debido a operaciones manuales ineficaces y capacidad limitada. La expansión del almacenamiento es esencial, pero conlleva pérdida de espacio y aumento de tiempos en operaciones (Salhieh & Alswaer, 2021). El problema del minifundio disminuyó la productividad agraria (Aspillaga et al., 2022).
En cuanto a la mejora en la gestión de inventarios, diversas investigaciones han implementado modelos efectivos. Por ejemplo, en una empresa se implementó un modelo de revisión periódica para reducir inventarios y evitar la falta de existencias. Se clasificaron los patrones de demanda utilizando el sistema ABC/XYZ, lo que permitió validar políticas de inventario, reduciendo las rotaciones anuales de 9,13 a 4,28, y aumentando la permanencia de 2,10 a 3,39 con inventario de seguridad. El stock real aumentó sus rotaciones de 3,02 a 4,31 anuales y redujo la permanencia de 6,65 a 3,90 eliminando el exceso de stock, lo que redujo costos totales, retrasos y mensualmente el número de piezas inventariadas, aumentando la disponibilidad de almacenamiento (Ternero et al., 2023).
Por otro lado, se planteó un sistema de control de inventarios en el área de almacén, el problema que aborda es la falta de un sistema de control de inventarios, este problema se identificó mediante el análisis de datos estadísticos, mostrando los productos faltantes, pérdidas de material, un sistema no actualizado con existencias físicas y demanda de emergencia. La solución propuesta en el artículo está basada en el establecimiento de un sistema de control de inventarios que utiliza métodos estadísticos, para su cálculo se utiliza la demanda promedio con el tiempo de demora de entrega del proveedor. Y así se utilizan las técnicas estadísticas para analizar los datos de inventario y detectar cualquier discrepancia entre las existencias físicas y las existencias registradas en el sistema almacén (Hernández et al., 2022).
Se identificaron los factores claves para mejorar la gestión de inventarios, donde el autor ha dividido la investigación en dos áreas claves, la situación actual de la empresa y la propuesta del marco, el escenario actual que tiene la compañía es de 57% de niveles máximos de inventarios, y para identificar los niveles óptimos de inventarios se desarrolló un marco Inventory drivers matriz (IDM), esto les permitió identificar los principales factores tanto internos como externos que influyen en los niveles de existencias, además los resultados revelaron que la empresa tenía una tendencia de excesos de existencias de productos terminados en los almacenes de sus filiales (Hansen et al., 2023).
En Ecuador, para un caso de estudio se implementó la metodología 5S, mediante el cual se abordaron problemas de falta de limpieza y organización en almacén, donde el 46.2% de los productos no estaban clasificados y faltaban procedimientos para el tratamiento de elementos innecesarios. Tras la implementación, se mejoró el orden y la limpieza en un 66%, con mejoras significativas en las etapas de clasificación, orden, limpieza, estandarización y disciplina (Ortiz-Sánchez et al., 2023). En una empresa agrícola, se implementó la gestión de inventarios para aumentar la productividad. Abordaron problemas de falta de control de inventario, clasificación, orden, supervisión, equipos y capacitación. Implementaron las 3S en el almacén con un cumplimiento del 94%. Tras la implementación completa, la productividad aumentó en un 15% (Velásquez et al., 2022).
En el estudio de Quiroz-Flores et al. (2023), implementaron un modelo de control de inventarios basado en Big Data, EOQ, ABC y Forecast en una PYME Ferretera para aumentar la productividad. Tras identificar un alto riesgo de fracaso por mala administración de inventarios, se aplicaron estrategias que mejoraron la eficiencia en un 11% con distribución diaria de órdenes de compra y en un 22% con automatización incluida. En (Aguilar-Paz et al., 2023), propusieron un modelo de gestión de inventarios para reducir las materias primas inmovilizadas en la industria textil mediante herramientas de ingeniería Lean. Tras identificar problemas como la lenta rotación de inventarios y altos costos asociados, se implementaron mejoras y se evaluó el impacto con el software Arena. Esto resultó en una rotación de inventarios incrementada en 0.83 veces y una notable reducción del stock inmovilizado en almacén, demostrando la efectividad del modelo propuesto.
En otros estudios, se evaluó el impacto del MRP en la gestión de inventarios de la panadería Rosmery mediante la recopilación de datos de demanda, producción y lista de materiales entre 2019 y 2020. El análisis histórico permitió comparar la eficiencia del sistema MRP, mostrando una reducción de costos de inventario de S/455 en comparación con S/13,050 del año anterior sin MRP. Además, facilitó la precisión en las cantidades de materiales necesarios para la producción de roscas (Gonzales-Abanto et al., 2022). Bonett et al. (2019), implementaron un sistema integrado de inventarios por pronósticos basado en la gestión del conocimiento en una PYME distribuidora, combinando la revisión periódica de inventarios y pronósticos para asegurar su sostenibilidad, tras un análisis de demanda y selección de modelos de abastecimiento, el sistema propuesto mejoró el nivel de servicio y pronóstico en un 25%, redujo la falta de inventario en un 74%, y disminuyó los costos adicionales en un 93%. La implementación en 10 productos categorizados con el modelo ABC demostró resultados óptimos en quiebres de stock e inventarios. Salazar et al. (2023), implementaron una gestión de inventarios para reducir costos, se utilizó un diseño experimental, analizando causas como espacios inadecuados y mala gestión de inventarios. Se aplicaron herramientas de ingeniería como layout de almacén, pronóstico de compra y método FIFO. Tras la implementación, se demostró en la estadística (p<0.05) con ahorros de $3947 en costos de compras, almacenamiento y administrativos.
La gestión de inventarios asegura el control y monitoreo del stock para cumplir con los pedidos a tiempo (Cruz, 2017). Así como también garantiza la disponibilidad de materia prima, productos terminados y repuestos en las condiciones y ubicaciones adecuadas, cumpliendo con calidad, plazos y cantidades requeridas (Arenal, 2020). Los inventarios son una lista organizada y detallada de todos los bienes de la organización (Álvarez & Parada, 2020). Son el número de artículos utilizados a lo largo de la cadena de abastecimiento para cumplir con los requerimientos de los clientes (Espejo, 2022). Los inventarios físicos son el recuento periódico de los artículos en almacén, considerando las existencias reales y no las contables, para identificar desigualdades por mercancías averiadas, robadas o confusión administrativa (Guerrero, 2009). También es la verificación y conteo físico de todas las unidades que la empresa tiene en almacén (Vidal, 2010).
Las 5S aumentan la eficiencia laboral mediante normas de organización y limpieza, facilitando encontrar productos en menos de un minuto y mejorando la seguridad y productividad, el procedimiento para la implementación de las 5S es el siguiente: Seiri (seleccionar), Seiton (organizar), Seiso (Limpieza), Seiketsu (Estandarizar) y Shitsuke (Seguimiento) (Socconini, 2021). La clasificación ABC es una herramienta que agrupa los productos en tres diferentes categorías A (80% de valor, mayor importancia), B (15% de valor, menor importancia), y C (5% de valor, mínima importancia). Esto permite destinar estrategias de almacenamiento y abastecimiento adecuadas. Está basada en la demanda anual de ventas categoriza como A (60-80% del valor de ventas, mayor inversión), B (20-30% del valor de ventas), y C (10% del valor de ventas, menor inversión). Los productos A y B requieren mayor control que los de categoría C.
Los días de inventario indican cuánto tiempo puede el inventario cubrir la demanda y la fórmula para su cálculo es inventario a la fecha entre demanda promedio. La capacidad de almacenamiento implica mantener un inventario de áreas utilizables para coordinar aprovisionamientos con compras, la fórmula para su cálculo es espacio utilizados entre capacidad total. El método de gestión de stock se utiliza para poder gestionar el stock de almacén, comúnmente se aplican dos tipos de stock, el stock mínimo y stock máximo. La productividad se refiere a los recursos utilizados, tanto humanos como no humanos, para producir bienes o servicios (Pérez, 2013). Evaluar la relación entre bienes producidos y recursos empleados y la fórmula empleada para su cálculo es eficiencia por eficacia. Para evaluar la eficiencia se empleó la fórmula entregas a tiempo entre pedidos cumplidos, y para eficacia pedidos cumplidos entre pedidos totales (Rodríguez, 2022).
La empresa agroindustrial AGROFRUTO, que se ha tomado como caso de estudio para el presente trabajo de investigación, se encuentra ubicada en Motupe, Lambayeque. Es una empresa productora, procesadora y exportadora de fruta (uva, arándano, palta y mango). Con más de 16 años en el rubro, la agroindustrial se ubica en el rubro de la comercialización nacional y la exportación a mercados europeos y norteamericanos. Desde hace unos años, su almacén de materia prima ha enfrentado problemas en los pedidos cumplidos. De los 5574 pedidos que le hicieron, solo cumplió con 3986, y los pedidos cumplidos a tiempo solo fueron 3015, estos problemas han llevado a que su productividad en su almacén sea solo del 54%. Esta problemática está conectada directamente con una mala gestión de inventarios existente referido a una serie de prácticas inadecuadas en la administración de los recursos dentro del almacén de AGROFRUTO, lo que afecta negativamente su eficiencia operativa. Además, se observan fallas en el control adecuado del stock de productos, lo que trae consecuencias de retrasos en las entregas, exceso o falta de inventario y pérdida de oportunidades de venta. Por esta razón, la presente investigación propone una mejora del rendimiento de productividad en el departamento de almacén de la agroindustria a través de una gestión de inventarios eficiente. Las mejoras se evidenciaron en el aumento de la productividad del almacén.
Por lo tanto, la presente investigación tuvo como objetivo general, implementar una gestión de inventarios para mejorar la productividad en el área de almacén de una empresa Agroindustrial Motupe, dicha gestión de inventarios redujo costos y mejoró la eficiencia, eficacia y por lo tanto productividad del almacén de materia prima.
2. Materiales y método
La investigación es de tipo aplicada con un alcance descriptivo, porque implica la evaluación y comparación de un problema práctico, interpretando conocimientos teóricos para mejorar el área de almacén de una empresa. Está investigación aplicada y descriptiva, evalúa la efectividad de las estrategias implementadas con diversas herramientas de mejora para solucionar problemas en la empresa. El diseño de esta investigación se distingue por ser tanto cuasiexperimental, integrando los métodos cuantitativos y cualitativos. Esta combinación permite obtener una comprensión completa al evaluar la eficacia de distintos enfoques, asegurando así una investigación exhaustiva y sólidamente fundamentada.
La población considerada son los productos despachados de almacén en el mes de diciembre 2023, enero y febrero del 2024. Como muestra se considera a la misma que la población dado que esta es el objeto de estudio. La técnica empleada para la recolección de datos fue la entrevista y el análisis documental, y el instrumento la guía de entrevista y la guía de análisis documental para ambas variables. Para analizar los datos se emplearon los programas de Microsoft Office Excel, para el análisis, tabulación, procesamiento y presentación de los datos recolectados a través de los instrumentos mencionados.
Los criterios éticos tomados en esta investigación fueron: la confidencialidad para brindar todas las condiciones de seguridad sobre la identidad de los trabajadores y empresa. Todos los datos empleados serán únicamente para fines de esta investigación. El criterio de veracidad para garantizar que los datos presentados son verdaderos, dado que la agroindustria brindo la información necesaria a los autores, y los instrumentos empleados fueron validados por tres expertos para su aprobación. Finalmente, el criterio de originalidad que permite garantizar el respeto de los derechos de los autores citados, además, se han referenciado conforme a las normas y estilos de redacción internacionales, asegurando un aporte único al campo de estudio.
3. Resultados
Mediante la utilización de herramientas como la entrevista, se logró obtener información detallada sobre los problemas que ocasionan la baja productividad. Para representar visualmente esta situación, se elaboró un diagrama de Ishikawa que muestra las doce causas principales que afectan los costos operativos de la empresa, como se observa en la Figura 1. Este diagrama permite identificar de manera clara y estructurada las áreas que requieren intervención, facilitando el análisis de las principales fuentes del problema.
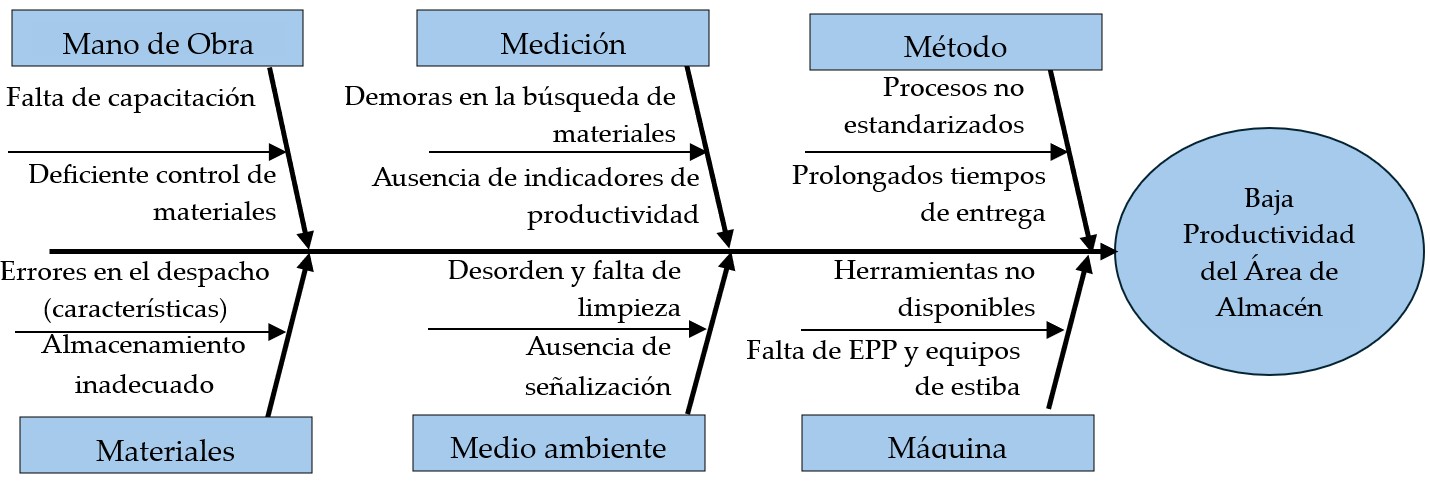
Figura 1. Diagrama de Ishikawa.
Tabla 1. Matriz de ponderación de las causas identificadas.
Cod. | Causas | Ocurrencias | Frec. Acum. | % Ocurrencias | % Frec. Acum. |
---|---|---|---|---|---|
C1 | Desorden y poca limpieza | 39 | 39 | 17.5% | 17.5% |
C2 | Ausencia de señalización | 34 | 73 | 15.2% | 32.7% |
C3 | Ausencia de indicadores de productividad | 33 | 106 | 14.8% | 47.5% |
C4 | Deficiente control de materiales | 32 | 138 | 14.3% | 61.9% |
C5 | Falta de capacitación | 28 | 166 | 12.6% | 74.4% |
C6 | Procesos no estandarizados | 11 | 177 | 4.9% | 79.4% |
C7 | Almacenamiento inadecuado | 10 | 187 | 4.5% | 83.9% |
C8 | Errores en el despacho (características) | 9 | 196 | 4.0% | 87.9% |
C9 | Demoras en la búsqueda de materiales | 9 | 205 | 4.0% | 91.9% |
C10 | Prolongados tiempos de entrega | 8 | 213 | 3.6% | 95.5% |
C11 | Falta de EPP y equipos de estiba | 6 | 219 | 2.7% | 98.2% |
C12 | Herramientas no disponibles | 4 | 223 | 1.8% | 100% |
Así mismo, se elaboró la matriz de ponderación de las doce causas que ocasionan el problema, con el fin de evaluar la magnitud de cada una de ellas en relación con su impacto en la productividad y los costos operativos. Esta evaluación cuantitativa permitió priorizar las causas más críticas, tal como se presenta en la Tabla 1. Estos datos proporcionan una base sólida para la toma de decisiones y para el diseño de estrategias de mejora enfocadas en las áreas de mayor impacto. Se determinó que, las principales causas que generan cerca del 80% de problemas está relacionado con desorden y poca limpieza (C1), ausencia de señalización (C2), ausencia de indicadores de productividad (C3), deficiente control de materiales (C4), falta de capacitación (C5) y procesos no estandarizados (C6). En la Tabla 2 se muestran las causas principales de la baja productividad en el área de almacén de materiales, junto con las herramientas de solución propuestas para cada una de ellas.
Tabla 2. Causas principales y herramientas de solución.
Cod. | Causas | Herramientas de solución |
---|---|---|
C1 | Desorden y poca limpieza | Diseño de 5S |
C2 | Ausencia de señalización | Diseño de 5S |
C3 | Ausencia de indicadores de productividad | Determinación de indicadores |
C4 | Deficiente control de materiales | Clasificación ABC y formatos de control de salida de materiales. |
C5 | Falta de capacitación | Plan de capacitaciones |
C6 | Procesos no estandarizados | Diseño de proceso de despacho |
3.1. Diagnóstico de la gestión de inventarios
Con un inventario de 69,250 unidades y una demanda promedio de 257 unidades durante los 3 meses, el inventario puede sostenerse durante aproximadamente 269.5 días antes de que se necesite reabastecer. En cuanto al uso del espacio, se observa que, en promedió durante los tres meses fue de 406.7 m², de los 600 m² del total de la capacidad del almacén. Esto quiere decir que, en promedio en los tres meses solo se usa el 68% de la capacidad del almacén (Tabla 3).
Tabla 3. Diagnóstico de la dimensión días de inventario y la capacidad de almacenamiento.
Mes | Semana | Inventario a la fecha | Demanda promedio | Días de inventario | Espacio utilizado (m2) | Capacidad de área (m2) | Cap. de almacén (%) |
---|---|---|---|---|---|---|---|
1 | 1 | 7312 | 80 | 91.4 | 400 | 600 | 67% |
2 | 5697 | 80 | 71.2 | ||||
3 | 7884 | 80 | 98.6 | ||||
4 | 5215 | 80 | 65.2 | ||||
2 | 1 | 5511 | 83 | 66.4 | 385 | 600 | 64% |
2 | 4624 | 83 | 55.7 | ||||
3 | 5864 | 84 | 69.8 | ||||
4 | 6677 | 85 | 78.6 | ||||
3 | 1 | 4696 | 84 | 55.9 | 435 | 600 | 73% |
2 | 6004 | 84 | 71.5 | ||||
3 | 4201 | 84 | 50.0 | ||||
4 | 5565 | 85 | 66.3 | ||||
Total | 69,250 | 257 | 269.5 |
El Stock mínimo en promedio de pallets que contienen materiales o herramientas es de 52.1, y el stock máximo en promedio en el almacén es de 104 pallets que se debe de mantener para evitar sobre saturar el almacén. Estos datos reflejan fluctuaciones tanto en los tiempos de entrega como en el consumo de productos, lo que lleva a ajustes en los niveles de inventario para garantizar la disponibilidad sin generar exceso de stock, tal como se describe en la Tabla 4.
Tabla 4. Diagnóstico de la dimensión gestión de stock.
Mes | Tiempo de entrega promedio | Consumo promedio de productos | Stock mínimo | Stock máximo | ||
---|---|---|---|---|---|---|
Días | Horas | Mensual | Horas | |||
1 | 14 | 336 | 1367 | 7 | 47.2 | 94.4 |
2 | 12 | 288 | 1454 | 8 | 38.0 | 76.1 |
3 | 18 | 432 | 1166 | 6 | 71.2 | 142.3 |
Promedio | 14.6 | 352 | 1329 | 7 | 52.1 | 104.3 |
Respecto de la dimensión productividad (Tabla 5), en promedio durante los tres meses la eficiencia fue de 76% con fluctuaciones entre el 68% y 90% en las semanas de cada mes. En cuanto a la eficacia fue del 71% que varía entre el 50% y 90%. Finalmente, la productividad, que es el indicador más crítico, el valor promedio es del 54% en el área de almacén de materiales.
Tabla 5. Diagnóstico de dimensión productividad.
Mes | Semana | Eficiencia | Eficacia | Productividad |
---|---|---|---|---|
1 | 1 | 80% | 50% | 40% |
2 | 68% | 70% | 48% | |
3 | 81% | 95% | 77% | |
4 | 75% | 75% | 56% | |
2 | 1 | 69% | 70% | 48% |
2 | 80% | 65% | 52% | |
3 | 69% | 90% | 62% | |
4 | 80% | 75% | 60% | |
3 | 1 | 85% | 70% | 60% |
2 | 70% | 70% | 49% | |
3 | 90% | 50% | 45% | |
4 | 69% | 75% | 52% | |
Promedio | 76% | 71% | 54% |
3.2. Implementación
Teniendo en cuenta las herramientas de solución descritas anteriormente, se determina que la implementación para presente estudio, contemplan un tiempo total de 2 meses (Tabla 6), en donde se aplican las herramientas: Metodología 5S, clasificación ABC, creación de formatos de control, indicadores, plan de capacitaciones y estandarizar proceso, con énfasis en mitigar causas raíz que afectan la eficiencia operativa.
Tabla 6. Cronograma de implementación de herramientas.
Etapa | Causa raíz a mitigar | Actividad | Marzo | Abril | ||||||
---|---|---|---|---|---|---|---|---|---|---|
S1 | S2 | S3 | S4 | S1 | S2 | S3 | S4 | |||
Metodología 5S | Desorden y poca limpieza, ausencia de señalizaciones | Conformación de comité | x | |||||||
Seiri (clasificar) | x | |||||||||
Seiton (ordenar) | x | |||||||||
Seiso (limpiar) | x | |||||||||
Seiketsu (estandarizar) | x | x | ||||||||
Shitsuke (mantener) | x | x | x | x | x | x | ||||
Clasificación ABC | Deficiente control de materiales | Identificación de los productos | x | |||||||
Identificación de las cantidades | x | |||||||||
Definición de los grupos ABC | x | |||||||||
Creación de formatos de control | Diseño y aplicación de formatos para control de materiales | x | ||||||||
Indicadores | Ausencia de indicadores de productividad | Diseño de indicadores | x | |||||||
Beneficios de indicadores | x | |||||||||
Plan de capacitaciones | Falta de capacitación | Identificación de temas y recursos | x | |||||||
Determinación de responsables y roles | x | |||||||||
Cronograma de ejecución | x | x | x | x | ||||||
Estandarizar proceso | Procesos no estandarizados | Diseño de proceso de despacho | x | |||||||
Documentación de proceso | x | |||||||||
Estandarización de proceso por jefatura | x | x |
3.2.1. Metodología 5S
En la primera S (Seiri) se empezó a identificar las existencias del almacén. Un total de 6065 productos fueron identificados, categorizando en los que eran necesarios e innecesarios, luego se evaluaron los productos en buen estado y mal estado. En la segunda S (Seiton) se organizaron los productos por un sistema de codificación, se definieron áreas y se señalaron las áreas del almacén. En la tercera S (Seiso) se empezó asignando las actividades de limpieza, luego se adquirió los materiales como paños, aspiradora, guantes, lejía, desengrasantes, escoba, recogedor, trapeador, cubetas y se ejecutó la limpieza. Por último, se designó el plan y cronograma anual de limpieza. En la cuarta S (Seiketsu) se establecieron las políticas y normas de orden y limpieza, y en la última S (Shitsuke) con el fin de asegurar que todos en el lugar de trabajos se comprometan a seguir los resultados, se realizaron capacitaciones sobre los temas (Introducción a la metodología 5s, aplicación de tarjetas rojas, un lugar en cada cosa, procesos de limpieza, reportes de incidencias), siendo el jefe de almacén el responsable de dichas capacitaciones.
Además, se realizó una evaluación detallada del cumplimiento de las 5S a lo largo del proceso, con el fin de medir la efectividad de la implementación de cada fase y asegurar que se mantuvieran los estándares establecidos. Esta evaluación se centró en observar el nivel de adopción y ejecución de las actividades relacionadas con la clasificación, organización, limpieza, estandarización y disciplina dentro del almacén. La evaluación de las 5S se contempló en las 6 semanas de aplicación del instrumento, con una calificación del 0 y 1, siendo el 0 que no cumplió, 1 que sí cumplió, teniendo en cuenta esta calificación se determinó que se cumplió Seiri a un 83,3%, Seiton en 83,3%, Seiso en 100%, Seiketsu en 100% y Shitsuke en 83,3% (Tabla 7).
Tabla 7. Resumen de los resultados de las 5S.
Evaluación | Área de almacén | Marzo | Abril | Total | Cumplimiento | ||||||
---|---|---|---|---|---|---|---|---|---|---|---|
S1 | S2 | S3 | S4 | S1 | S2 | S3 | S4 | ||||
Seiri (Clasificar) | Se cumplen los criterios de evaluación de clasificación de los materiales y herramientas | - | - | 1 | 1 | 1 | 0 | 1 | 1 | 5 | 83.3% |
Seiton (Ordenar) | Se cumplen los criterios de evaluación del orden de los materiales y herramientas | - | - | 1 | 1 | 1 | 1 | 0 | 1 | 5 | 83.3% |
Seiso (Limpiar) | Se cumplen los criterios de evaluación de limpieza | - | - | 1 | 1 | 1 | 1 | 1 | 1 | 6 | 100% |
Seiketsu (Estandarizar) | Se cumplen los criterios de evaluación de estandarización | - | - | 1 | 1 | 1 | 1 | 1 | 1 | 6 | 100% |
Shitsuke (Disciplina) | Se cumplen los criterios de evaluación disciplina | - | - | 1 | 0 | 1 | 1 | 1 | 1 | 5 | 83.3% |
3.2.2. Clasificación ABC
La implementación de un sistema de clasificación ABC ayuda a optimizar la gestión y el control de los productos según su importancia y frecuencia de uso. En la Tabla 8, se determina que existen un total de 2253 productos en el área de almacén distribuidos en 9 grupos con diferentes cantidades asignadas a cada tipo de material, lo que ayuda a establecer una organización adecuada para el control de inventarios.
Tabla 8. Identificación de los productos y cantidades.
Tipo de material | Cantidad |
---|---|
Construcciones y obras en curso | 832 |
Materiales de construcción | 630 |
Repuestos de maquinaria de planta | 239 |
Tuberías, válvulas y conexiones para agua y gases | 200 |
Combustibles, aceites, lubricantes y gases | 147 |
Mecanismos y accesorios eléctricos | 98 |
Suministros diversos | 92 |
Soldaduras e implementos para soldar | 12 |
Accesorios y suministros de riego | 3 |
Total | 2253 |
Se determina que el 75.5% de productos principales para la empresa, que se categorizan en el grupo “A” son las construcciones y obras en curso, materiales de construcción y repuestos de maquinaria de planta. Por su parte, los materiales que se encuentran en el grupo “B” (representando el 15.4%) son las tuberías, válvulas y conexiones para agua y gases, y, combustibles, aceites, lubricantes y gases. Por último, los materiales que se encuentran en el grupo “C” (representando el 9.1%) son mecanismos y accesorios eléctricos, suministros diversos, soldaduras e implementos para soldar y accesorios y suministro de riego (Tabla 9).
Tabla 9. Definición de los grupos ABC y frecuencias para cada tipo de material.
Tipo de material | Cant. | Cant. acumulada | % | % acumulado | Zona | % |
---|---|---|---|---|---|---|
Construcciones y obras en curso | 832 | 832 | 36.9% | 36.9% | A | 75.5% |
Materiales de construcción | 630 | 1462 | 28.0% | 64.9% | ||
Repuestos de maquinaria de planta | 239 | 1701 | 10.6% | 75.5% | ||
Tuberías, válvulas y conexiones para agua y gases | 200 | 1901 | 8.9% | 84.4% | B | 15.4% |
Combustibles, aceites, lubricantes y gases | 147 | 2048 | 6.5% | 90.9% | ||
Mecanismos y accesorios eléctricos | 98 | 2146 | 4.3% | 95.3% | C | 9.1% |
Suministros diversos | 92 | 2238 | 4.1% | 99.3% | ||
Soldaduras e implementos para soldar | 12 | 2250 | 0.5% | 99.9% | ||
Accesorios y suministro de riego | 3 | 2253 | 0.1% | 100% | ||
Total | 2253 | 100% | 100% |
3.2.3. Creación de formatos de control
El método de control de inventario en el cual se registran los datos referentes a la mercadería, los saldos, las entradas y las salidas se presenta en la Tabla 10. Gracias al diseño y aprobación del presente formato por parte de jefatura, se logra múltiples beneficios para el área, como una mayor precisión en el registro de inventarios, ya que al contar con un formato estandarizado se minimizan los errores humanos y se asegura que todos los datos relevantes sean capturados de manera consistente. Esto también permite una mejor toma de decisiones, ya que el personal encargado puede contar con información actualizada sobre las existencias, salidas y entradas de productos, facilitando la gestión de reabastecimiento. Además, la optimización del tiempo es otro beneficio importante, ya que el proceso de actualización y revisión de inventarios se vuelve más eficiente. Esto, a su vez, facilita las auditorías y el control interno al disponer de registros organizados, mejorando la trazabilidad de productos y contribuyendo a una gestión más efectiva del stock.
Tabla 10. Formato para control de entrada y salida de materiales.
Empresa Agroexportadora Agrofruto |
![]() |
|||||||||
---|---|---|---|---|---|---|---|---|---|---|
Reporte de control de inventarios | Código | ITR-MARC-02 | ||||||||
Revisión | dd/mm/aaaa | |||||||||
Aprobado por | Supervisor | |||||||||
Detalle | ||||||||||
N° | Descripción del Material | Cant. | Unidades actuales | Ubicación en almacén | Fecha | Solicitado por | Cantidad | Cantidad total | ||
Entrada | Salidad | Entrada | Salidad | |||||||
Cargo: | Firma del responsable |
3.2.4. Indicadores de gestión de almacenes
Se han diseñado 5 indicadores, los cuales ayudan a tener un control más eficiente de los productos del área de almacén de materiales y herramientas. Para cada uno de los indicadores, se presenta la expresión matemática, descripción, justificación y beneficios (Tabla 11). Gracias al diseño de estos indicadores de gestión en el almacén de materiales y herramientas, se logra mejorar la visibilidad y control del inventario, permitiendo una gestión más efectiva al reducir costos y optimizar la inversión en stock. Mejorar la satisfacción del cliente interno al asegurar la precisión y disponibilidad de los productos. Además, facilitar el cumplimiento de estándares de auditoría y regulaciones.
Tabla 11. Diseño de indicadores para el almacén.
Indicador | Elementos | Detalle |
---|---|---|
Rotación de Inventario | Fórmula | |
Descripción | Mide las veces que el inventario se vende y reemplaza en un periodo. | |
Justificación | Indica eficiencia en la gestión de stock. | |
Beneficios | Optimiza espacio y reduce costos de almacenamiento. | |
Días de inventario | Fórmula | |
Descripción | Promedio de días que la mercancía está en almacén. | |
Justificación | Refleja la liquidez del inventario. | |
Beneficios | Previene sobre inventarios o faltantes. | |
Costo de Almacenamiento | Fórmula | |
Descripción | Porcentaje del costo de mantener el inventario. | |
Justificación | Muestra el impacto del almacenamiento en costos. | |
Beneficios | Identifica oportunidades de reducción de costos. | |
Nivel de Servicio | Fórmula | |
Descripción | Capacidad de satisfacer pedidos con stock disponible. | |
Justificación | Esencial para la satisfacción del cliente. | |
Beneficios | Mejora relación con cliente y reputación de la empresa. | |
Tiempo de Reposición | Fórmula | |
Descripción | Tiempo necesario para reponer inventario. | |
Justificación | Clave para planificación de compras. | |
Beneficios | Asegura disponibilidad continua de productos. |
3.2.5. Estandarización de proceso por jefatura
Tabla 12. Estandarización de proceso por jefatura.
Empresa Agroexportadora Agrofruto |
![]() |
|
---|---|---|
PROCEDIMIENTO DE TRABAJO | ||
Código: PT-CA-GL-01 | Descripción: Manual de procedimiento de trabajo para el proceso de despacho | |
Procedimiento estandarizado del proceso de despacho | ||
I. Introducción | ||
La empresa agroexportadora se ubica en Motupe, Lambayeque, se destaca en la producción de arándanos, aunque también cultiva uvas y espárragos. El estudio se realiza en el almacén de materiales y herramientas, de lo cuál se va a definir el proceso de despacho de dichos objetos, lo cual sus actividades comienzan desde la recepción del orden de pedido hasta el destino final de los mismos. Por ello se realiza el documento, para estandarizar dichos procesos integrados con el despacho de materiales y herramientas con el fin de optimizar dichos procesos y mejorar la eficiencia del área. |
||
II. Objetivo | ||
Establecer procedimientos estandarizados de actividades para el proceso de despacho de herramientas y materiales en el área de almacén. |
||
III. Objetivos específicos | ||
|
||
IV. Alcance | ||
El presente documento tiene por alcance a todo el proceso de actividades de despacho de herramientas y materiales en el área de almacén de la empresa agroexportadora en Motupe. |
||
V. Definiciones | ||
Se presentan las definiciones de términos que tiene el presente documento:
|
||
VI. Responsables | ||
|
||
VII. Documentos relacionados | ||
Dentro de la estandarización del proceso de despacho de herramientas y materiales, se presentan documentos como orden de despacho, guías de remisión, facturas y documentos de exportación si es necesario. |
||
VIII. Proceso de despacho | ||
![]() |
||
IX. Métricas de control | ||
El proceso de despacho debe cumplir con parámetros, los cuales se dan por los siguientes: (i) Calidad de las herramientas y materiales, (ii) Embalaje adecuado, (iii) Tiempo de ciclo de despacho, (iv) Utilización de recursos, (v) Porcentaje de órdenes despachadas. |
3.3 Resultados de la gestión de inventarios post implementación
Se presenta en la Tabla 13, la mejora de la variable independiente y dependiente. Posterior a la aplicación de las herramientas de mejora se recopiló los datos de la gestión de inventarios, para evaluar su mejora. Con un inventario de 85,217 unidades y una demanda promedio de 250 unidades en los 3 meses evaluados. Esta demanda promedio parece ser constante, lo que indica una demanda estable de los productos en el almacén. El inventario, en promedio dura aproximadamente 341.6 días antes de que se necesite reabastecer. Esto sugiere que, en general, el inventario está bien equilibrado para cubrir la demanda durante los próximos días. Aunque la demanda promedio se mantiene constante, el uso del espacio ha aumentado con el tiempo, alcanzando casi el 100% de la capacidad en el tercer mes. Esto podría sugerir que, si la tendencia continúa, el almacén podría necesitar expansión o ajustes para evitar problemas de capacidad en el futuro.
Tabla 13. Resultados de la gestión de inventarios y capacidad de almacenamiento.
Mes | Semana | Inventario a la fecha | Demanda promedio | Días de inventario | Espacio utilizado (m2) | Capacidad de área (m2) | Capacidad de almacenamiento (m2) |
---|---|---|---|---|---|---|---|
1 | 1 | 6185 | 82 | 75.4 | 500 | 600 | 83% |
2 | 7470 | 84 | 88.9 | ||||
3 | 6520 | 84 | 77.6 | ||||
4 | 7022 | 83 | 84.6 | ||||
2 | 1 | 7010 | 83 | 84.5 | 530 | 600 | 88% |
2 | 7591 | 82 | 92.6 | ||||
3 | 7749 | 83 | 93.4 | ||||
4 | 7806 | 84 | 92.9 | ||||
3 | 1 | 7908 | 84 | 94.1 | 580 | 600 | 97% |
2 | 6667 | 84 | 79.4 | ||||
3 | 6507 | 83 | 78.4 | ||||
4 | 6782 | 82 | 82.7 | ||||
Total | 85,217 | 250 | 82.7 |
El Stock mínimo de pallets que contienen materiales o herramientas es de 31.5, y el stock máximo en el almacén es de 63.1 pallets que se debe de mantener para evitar sobre saturar el almacén (Tabla 14).
Tabla 14. Gestión de stock.
Mes | Tiempo de entrega promedio | Consumo promedio de productos | Stock mínimo | Stock máximo | ||
---|---|---|---|---|---|---|
Días | Horas | Mensual | Horas | |||
1 | 16 | 384 | 1686 | 9 | 43.7 | 87.4 |
2 | 12 | 288 | 2022 | 11 | 27.3 | 54.7 |
3 | 10 | 240 | 1959 | 10 | 23.5 | 47.0 |
Promedio | 12.67 | 304 | 1889 | 10 | 31.5 | 63.1 |
En los últimos tres meses, los resultados en promedio para la eficiencia fueron de 94% y la eficacia fue del 91%, dando una productividad del 85% en el área de almacén de materiales y herramientas. Esto quiere decir que, en un 85% el almacén logró entregar los productos planificados en el tiempo que corresponde (Tabla 15).
Tabla 15. Resultados de la productividad..
Mes | Semana | Eficiencia | Eficacia | Productividad |
---|---|---|---|---|
1 | 1 | 78% | 80% | 62% |
2 | 82% | 88% | 72% | |
3 | 89% | 82% | 73% | |
4 | 92% | 75% | 69% | |
2 | 1 | 97% | 92% | 89% |
2 | 97% | 95% | 92% | |
3 | 100% | 98% | 98% | |
4 | 96% | 100% | 96% | |
3 | 1 | 96% | 89% | 85% |
2 | 95% | 98% | 93% | |
3 | 100% | 95% | 95% | |
4 | 100% | 98% | 98% | |
Total | 94% | 91% | 85% |
En la Figura 2, muestra una comparación entre el pre-test y el post-test en las tres categorías analizadas para la eficiencia, eficacia y productividad. En la categoría eficiencia, se observa una mejora del 17%, pasando del 76% al 94%; en eficacia, la mejora es del 20%, pasando del 71% al 91%; y en productividad, se registra una mejora del 31%, incrementando del 54% al 85%. La línea verde en la figura ilustra el porcentaje de mejora entre ambos test para cada categoría, destacando un impacto positivo significativo de las intervenciones o cambios aplicados.
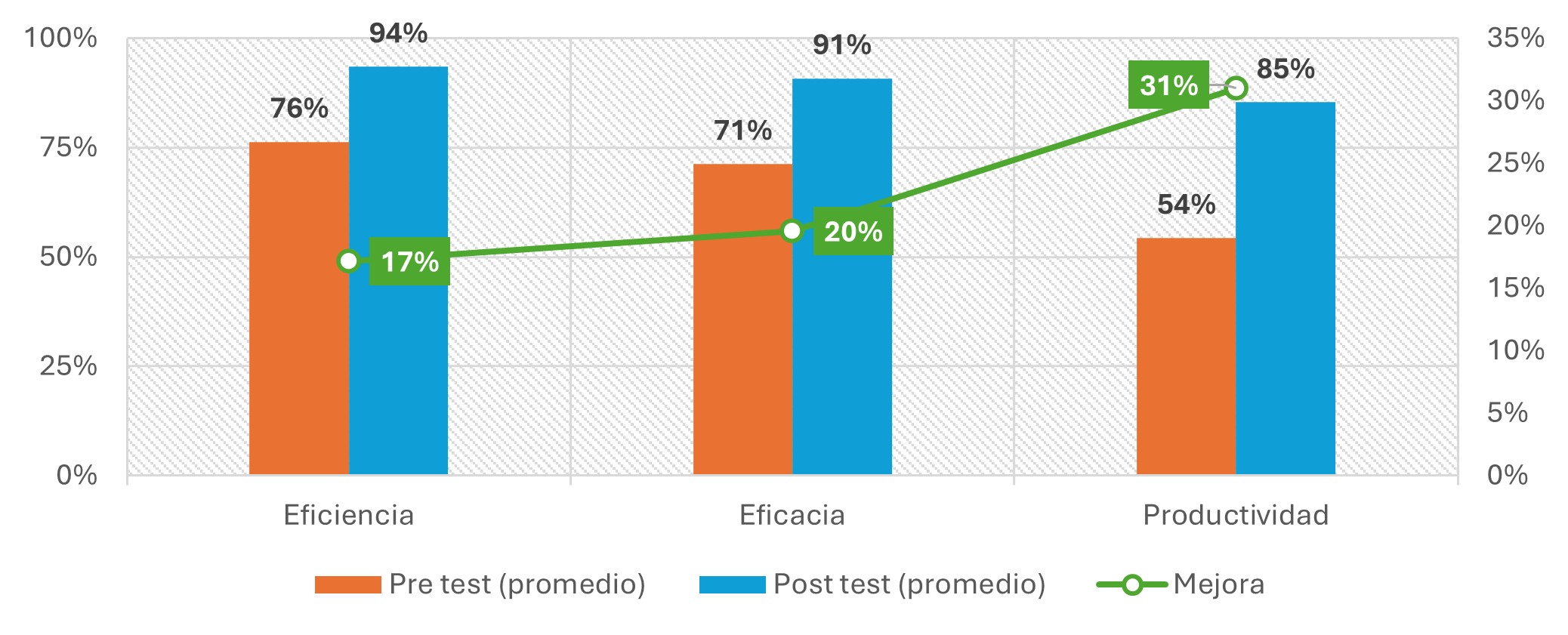
Figura 2. Análisis de la mejora de la productividad..
3.4 Costo-Beneficio
Para determinar el beneficio costo, se empleó la siguiente fórmula
El cálculo de los beneficios, se analizaron durante los tres meses tanto el ahorro generado por la reducción de costos debido a errores en la preparación de pedidos, que asciende a S/. 11,845.19, como el aumento en la ganancia neta derivada de la mayor producción, que es de S/. 123,981.90. Al sumar estos valores, se obtiene el beneficio total de S/. 135,827.09.
En cuanto a los costos proyectados, el costo de almacenamiento para los próximos tres meses es de S/. 85,009.50. El costo actual de preparación de pedidos es de S/. 17,938.80, mientras que el costo total de inversión se estima en S/. 12,255.00. El monto del costo total de inversión incluye gastos relacionados con la capacitación en 5S, mano de obra para la implementación de 5S, herramientas y equipos para la zona de producción, así como los costos indirectos de inversión y otros gastos asociados con la implementación.
El análisis de la inversión realizada muestra que, por cada sol invertido durante los tres meses evaluados, se obtuvo una ganancia de S/. 0.18.
4. Discusiones
Para la presente investigación, se implementó una gestión de inventarios para mejorar la productividad en el área de almacén de una empresa agroindustrial Motupe. Realizada la implementación de las herramientas de mejora se tiene que el inventario dura 341.6 días antes de ser reabastecidos, la capacidad del almacén es de 89% y el stock mínimo que se debe tener es de 31.5 pallets y el máximo es 639.1 pallets, logrando aumentar la productividad de 54% a 81% en un periodo de dos meses, esto equivale al aumentó del 31% de la productividad del almacén de materiales, teniendo relación con el articulo (Pérez-Mata & Romero-Dessens, 2022), donde también se implementó un sistema de gestión de inventario logrando reducir el 50% de inventario deteriorado, el tiempo de salida de productos del almacén a producción ahora es de 15 días y la capacidad del almacén aumento y ahora solo se utiliza 573 m2. También en el artículo (Velásquez et al., 2022), se implementó una gestión de inventarios para lograr incrementar la productividad, presentaba problemas de orden, clasificación, limpieza, rotura de stock, bajo control de calidad, personal no capacitado, luego de la implementación se mejoró en un 15% la productividad.
Empleando la técnica de entrevista y análisis documentario, se logró reconocer los problemas en la gestión de inventarios que ocasionan la baja productividad en la agroindustrial, con el diagrama de Ishikawa, análisis de Pareto y matriz de priorización se reconocieron las 6 principales causas que ocasionan dichos problemas como desorden y poca limpieza, ausencia de señalización, ausencia de indicadores de productividad, deficiente control de materiales, falta de capacitación y procesos no estandarizados, lo que lleva a tener relación con la investigación (Gonzales-Abanto et al., 2022), quien empleó como técnicas, el análisis documentario y la entrevista para conocer la problemática actual que proviene de no conocer las cantidades de productos almacenados y la falta de categorización de estos. Estos problemas se presentan también en la investigación (Salazar et al., 2023), quienes también hicieron uso las herramientas de Ishikawa y Pareto para conocer la problemática actual en la empresa, identificando problemas de falta de orden y limpieza en el almacén, mala clasificación de productos, pérdida de productos por el polvo.
Con la implementación de las 5S, ABC, plan de capacitación, diseños de proceso de despacho en el almacén de materiales, determinación de indicadores, formatos de control de salida de materiales, se tiene como consecuencia mayor agilidad en el despacho de productos, pasando de un tiempo de 39 minutos a 31 minutos, aumentando el nivel de productividad de 54% a 81%, también se realizó el análisis beneficio – costo, donde se obtuvo como resultado S/. 1.18, esto quiere decir que por cada sol que la agroindustrial invierta se obtiene de beneficio S/. 0.18 lo que significa que la propuesta es beneficiosa para la agroindustria, teniendo relación con trabajo de investigación (Quiroz-Flores et al., 2023), donde también implementaron las 5S y la distribución del almacén a través del método ABC, lo cual resultó en el aumento de la productividad, Para lograr esto, se realizó una comparación entre la situación anterior y posterior a la implementación de las propuestas, teniendo un aumento del 11% en su eficiencia. También en el artículo (Ortiz-Sánchez et al., 2023), se implementó la metodología 5s, dado que presentaban el 42% de sus productos desorganizados, además tenían problemas de limpieza en el almacén, luego de su implementación se tuvo 66% de mejora en orden y limpieza.
Los autores deben analizar los resultados y cómo pueden ser interpretados en relación con estudios previos y las hipótesis de trabajo. Los descubrimientos y sus implicaciones deben ser examinados dentro de un contexto lo más amplio posible. Además, es recomendable señalar posibles direcciones para futuras investigaciones. Es esencial que los autores analicen los resultados obtenidos y los comparen con los de estudios anteriores, destacando tanto las similitudes como las diferencias. Este análisis debe incluir una evaluación crítica de cómo los hallazgos apoyan o desafían las hipótesis de trabajo. Los autores deben considerar las implicaciones de sus resultados no solo para su campo específico de estudio, sino también en relación con otras disciplinas relevantes.
Además, es importante identificar las limitaciones del estudio y cómo estas podrían influir en la interpretación de sus resultados. Esto proporcionará una base sólida para las conclusiones presentadas y ayudará a orientar investigaciones futuras. Resaltar direcciones potenciales para futuras investigaciones es crucial, ya que puede inspirar nuevos estudios que aborden preguntas no resueltas o que amplíen el conocimiento existente en el campo.
5. Conclusiones
Utilizando el diagrama de Ishikawa, la matriz de correlaciones y el diagrama de Pareto, se identificó las principales causas de la baja productividad en el almacén de herramientas y materiales de la empresa agroindustrial Motupe, las cuales fueron el desorden y falta de limpieza, la ausencia de señalización, la falta de indicadores de productividad, mal control de materiales, falta de capacitación y procesos no estandarizados. En cuanto al diagnóstico de inventarios, se registró un total de 69,250 unidades con una demanda promedio de 257 unidades en los últimos tres meses. Esto significa que el inventario dura 269,5 días antes de necesitar reabastecimiento. La capacidad de almacenaje del almacén de materiales es del 68%, con un stock mínimo de 52,1 palets y un máximo de 104 palets para evitar la saturación. En términos de productividad, durante los últimos tres meses la eficiencia fue del 76%, la efectividad del 71% y determinando la baja productividad que fue del 54% en el área de almacén de materiales.
Con la implementación de la metodología 5S se logró una mejora notable en la organización, orden y disciplina del almacén de materiales alcanzando el 83,3%, y en limpieza y estandarización alcanzando el 100%. Además, se utilizó la clasificación ABC para organizar los materiales. En el grupo “A” se encuentran las construcciones y obras en curso, materiales de construcción y repuestos para maquinaria de planta. El grupo "B" incluye tuberías, válvulas y conexiones para agua y gases, así como combustibles, aceites, lubricantes y gases. El grupo "C" contiene mecanismos y accesorios eléctricos, insumos diversos, implementos para soldar y soldar, y accesorios e insumos para riego. Se establecieron formatos para registrar la entrada y salida de materiales y se implementaron indicadores de gestión de almacén, como rotación de inventario, días de inventario, costo de almacenamiento, nivel de servicio y tiempo de reabastecimiento, para mejorar el control de productos.
Se diseñó un plan de capacitación que aborda temas como procesos de despacho efectivos, uso de software de gestión de almacenes Nisiran, técnicas de empaque y etiquetado, normas de seguridad en el despacho, atención al cliente y resolución de incidentes. Además, se estandarizó el proceso de despacho. Gracias a estas mejoras en la gestión de inventarios, los pedidos cumplidos en almacén aumentaron hasta los 5.667 palets. La productividad también mostró una mejora significativa en los últimos tres meses, con una eficiencia del 94% y una efectividad del 91%, resultando en una productividad del 85% en el área de almacén de materiales y herramientas de la empresa agroindustrial.
Se determinó que el costo total de implementación de la gestión de inventarios fue de S/12,255.00, incluyendo capacitación 5S, mano de obra, herramientas y equipos para la producción, costos de inversión indirecta y otros gastos de implementación. El costo proyectado de almacenamiento para los próximos tres meses es de S/85,009.50. Además, se calculó el costo actual por error en la preparación del pedido, el cual asciende a S/17,938.8. Sin embargo, la reducción de estos errores generó un ahorro de S/11,845.19. La producción total de aguacate fue de 16 mil 531 unidades, lo que arrojó una utilidad neta de S/123,981.90. Gracias a la inversión realizada la empresa obtuvo una utilidad de S/0.18 por cada sol invertido en los tres meses evaluados.
Por último se concluye que en la gestión de inventarios, se implementaron las metodologías 5S para mejorar el orden y limpieza, la metodología ABC y la creación de formatos de control para tener un buen control de los materiales, además se implementaron indicadores de productividad para poder medir constantemente la gestión de inventarios, se realizó un plan de capacitaciones y se estandarizaron procesos, con esta implementación de gestión de inventarios la eficiencia mejoró en un 17%, la eficacia mejoró en un 20% y la productividad mejoró en un 31%.
Contribuciones: Conceptualización, metodología, validación, análisis formal, investigación, redacción del borrador original, escritura, revisión y edición, visualización, supervisión, administración del proyecto, N.Y.B.-C. y L.F.-R. Todos los autores han leído y están de acuerdo con la versión publicada del manuscrito.
Conflicto de Intereses: Los autores declaran no tener conflictos de interés.
Agradecimientos: No aplica.
Referencias
- Aguilar-Paz, A., Bellido-Yarlque, J., Quiroz-Flores, J. C., & S, N. (2023). A Proposed Model for Inventory Management to Minimize the Rate of Raw Materials Tied up of Textile Industry with Lean Engineering Tools. International Journal of Mechanical Engineering, 10(8), 11–20. https://doi.org/10.14445/23488360/IJME-V10I8P102
- Alnaim, M., & Kouaib, A. (2023). Inventory Turnover and Firm Profitability: A Saudi Arabian Investigation. Processes, 11(3), Article 3. https://doi.org/10.3390/pr11030716
- Álvarez, L. F., & Parada, S. P. (2020). Gestión de inventarios: Cartilla para el aula. Corporación Universitaria Minuto de Dios. https://elibro.net/es/ereader/bibsipan/198393?page=1
- Arenal, C. (2020). Gestión de inventarios: UF0476. Editorial Tutor Formación. https://elibro.net/es/ereader/bibsipan/126745?page=1
- Aspillaga, J. O. D. V., Mann, G. A. L. B., & Altamirano, L. S. W. (2022). Políticas públicas y desarrollo agrario en el Perú: Un enfoque de planeamiento estratégico. Revista Latinoamericana de Difusión Científica, 4(7). https://doi.org/10.38186/difcie.47.07
- Baca, J., Sánchez, F., Castro, P., Marcelo, E., & Alvarez, J. C. (2021). Productivity Improvement In Companies of A Wooden Furniture Cluster In Peru. International Journal of Engineering Trends and Technology, 69(10), 97–107. https://doi.org/10.14445/22315381/IJETT-V69I10P213
- Bandopadhyay, K., & Khan, T. L. (2020). Factors of Export Promotion of MSME in India with Special Reference to Raw Material Availability. SEDME (Small Enterprises Development, Management & Extension Journal), 47(1), 17–32. https://doi.org/10.1177/0970846420930446
- Bonett, J., Silva, L., Viacava, G., & Raymundo, C. (2019). Sistema integrado de inventarios por pronósticos basado en la gestión del conocimiento para la disminución de los quiebres de stock en una PYME distribuidora. Proceedings of the 17th LACCEI International Multi-Conference for Engineering, Education, and Technology: “Industry, Innovation, and Infrastructure for Sustainable Cities and Communities”. https://doi.org/10.18687/LACCEI2019.1.1.34
- Cardoso, E. P., Molina, D. G. A., Lugo, R. E. M., & Guzmán, R. A. (2023). Gestión de inventarios en microempresas del sector farmacéutico, Colombia. Revista Venezolana de Gerencia, 28(9),. https://doi.org/10.52080/rvgluz.28.e9.29
- Cruz, A. (2017). Gestión de inventarios. IC Editorial. https://elibro.net/es/ereader/bibsipan/59186?page=1
- Espejo, M. (2022). Gestión de inventarios: Métodos cuantitativos. Marge Books. https://elibro.net/es/ereader/bibsipan/217920?page=1
- Gonzales-Abanto, W., Quispe-Vasquez, L., Carrion-Mosqueira, I., Castrejon-Atalaya, M., Leiva-Roncal, D., Villar-Muñoz, P., & Mostacero-Baca, Z. (2022). Impact of the MRP technique on the Inventory Management of the Rosmery Bakery in the City of Cajamarca. Proceedings of the 20th LACCEI International Multi-Conference for Engineering, Education and Technology: “Education, Research and Leadership in Post-pandemic Engineering: Resilient, Inclusive and Sustainable Actions”. https://doi.org/10.18687/LACCEI2022.1.1.232
- Guerrero, H. (2009). Inventarios: Manejo y control. Ecoe Ediciones. https://elibro.net/es/ereader/bibsipan/69078?page=1
- Hansen, Z. N. L., Andreu, C. M., Khan, O., Haug, A., Hvam, L., & Hansen, N. E. (2023). Identification of key drivers for improving inventory management in pharmaceutical supply chains. Production Engineering, 17(5), 763–772. https://doi.org/10.1007/s11740-023-01199-2
- Hernández, L. M., Orencio, M. C. M., Barrales, R. R., Pérez, V. U. V., López, P. de A., & Franco, V. H. J. (2022). Aplicación de seis sigma en una empresa de mantenimiento industrial para reducir el número de licitaciones incorrectas. South Florida Journal of Development, 3(2), 2826–2837. https://doi.org/10.46932/sfjdv3n2-097
- Ortiz-Sánchez, E., García-Castro, W., Ramos-Alfonso, Y., Ortiz-Sánchez, E., García-Castro, W., & Ramos-Alfonso, Y. (2023). Propuesta de mejora continua mediante la aplicación de una metodología en una planta camaronera. Ingeniería Industrial, 44(3), 42–58.
- Peña-Asenjo, S., Castañeda-Chinchay, D., & Fontenla-Gambini, L. (2023). Inventory management and its relationship with production planning in a textile company. LACCEI, 1(8). https://doi.org/10.18687/LACCEI2023.1.1.122
- Pérez, M. D. (2013). Herramientas de medida de la productividad. Editorial ICB. https://elibro.net/es/lc/bibsipan/titulos/113014
- Pérez-Mata, C. E., & Romero-Dessens, L. F. (2022). Implementation of an inventory management system to improve the material flow of expanded polystyrene (EPS) products. Proceedings of the 20th LACCEI International Multi-Conference for Engineering, Education and Technology: “Education, Research and Leadership in Post-pandemic Engineering: Resilient, Inclusive and Sustainable Actions”.. https://doi.org/10.18687/LACCEI2022.1.1.554
- Quiroz-Flores, J. C., Caceres-Paitan, D., & Avila-Nolasco, R. (2023). Inventory control model based on Big Data, EOQ, ABC and forecast to increase productivity in a hardware SME. Proceedings of the 2023 14th International Conference on E-Education, E-Business, E-Management and E-Learning, 271–275. https://doi.org/10.1145/3588243.3588245
- Rodríguez, D. C. (2022). La productividad en el servicio. Editorial UPTC. https://elibro.net/es/ereader/bibsipan/231879?page=1
- Salas-Navarro, K., Maiguel-Mejía, H., Acevedo-Chedid, J., Salas-Navarro, K., Maiguel-Mejía, H., & Acevedo-Chedid, J. (2017). Inventory Management Methodology to determine the levels of integration and collaboration in supply chain. Ingeniare. Revista chilena de ingeniería, 25(2), 326–337. https://doi.org/10.4067/S0718-33052017000200326
- Salazar, J. J., Castillo, S. E., Miñan, G. S., & Valderrama, M. W. (2023). Implementación de la Gestión de Inventarios para la Reducción de los Costos en una Empresa Agroindustrial, Olmos – Perú. 216–221. https://doi.org/10.54808/CICIC2023.01.216
- Salhieh, L., & Alswaer, W. (2021). A proposed maturity model to improve warehouse performance. International Journal of Productivity and Performance Management, 71(8), 3724–3746. https://doi.org/10.1108/IJPPM-01-2021-0043
- Socconini, L. (2021). Lean Six Sigma White Belt: Aplica las herramientas que están transformando el mundo empresarial. Marge Books. https://elibro.net/es/ereader/bibsipan/198577?page=79
- Stopková, M., Stopka, O., & Ľupták, V. (2019). Inventory Model Design by Implementing New Parameters into the Deterministic Model Objective Function to Streamline Effectiveness Indicators of the Inventory Management. Sustainability, 11(15), Article 15. https://doi.org/10.3390/su11154175
- Ternero, R., Sepulveda-Rojas, J. P., Alfaro, M., Fuertes, G., & Vargas, M. (2023). Inventory Management With Stochastic Demand: Case Study Of A Medical Equipment Company. The South African Journal of Industrial Engineering, 34(1), Article 1. https://doi.org/10.7166/34-1-2668
- Velásquez, C. V. I., Blas, C. B. S., Tiravantti, L. M. V., & Castellares, R. M. Q. (2022). Gestión de inventarios para incrementar la productividad en una empresa agrícola. INGnosis, 8(2). https://doi.org/10.18050/ingnosis.v8i2.2475
- Vidal, C. J. (2010). Fundamentos de control y gestión de inventarios. Programa Editorial Universidad del Valle. https://elibro.net/es/ereader/bibsipan/128995?page=1
-
Este artículo es de acceso abierto distribuido bajos los términos y condiciones de la Licencia Creative Commons Attribution (CC BY) (https://creativecommons.org/licenses/by/4.0/)
- Cómo citar: Becerra-Carrillo, N.Y. y Fernández-Ramos, L. (2025). Mejora de la Productividad en el Área de Almacén mediante la Gestión de Inventarios en una Empresa Agroindustrial de Motupe. Epistemia Revista Científica, 9(1), 1–17. https://doi.org/10.26495/erc.2780